Why So Many Medical Device Companies Lack Real-Time Traceability and Visibility
Table of Contents
How long would it take a stakeholder at your company to identify and understand the new and changed requirements in your current product version compared to the previous one? If the answer is anything other than “a few seconds,” your business is likely overburdened by complexity that is slowing growth.
Without real-time visibility and end-to-end traceability, MedTech organizations simply don’t have an accurate picture of their current state of operations and product development. It’s like driving with foggy windows — it's hard to see where you are and where you're going, which means you might make a wrong turn that takes the business in a bad direction and could even end up harming people.
Here’s why real-time visibility and traceability are required to stay competitive in today’s MedTech market, plus tips on how automated system connectedness can get you there.
Transforming MedTech with real-time visibility and traceability
First, let’s take a look at how leading MedTech companies define these concepts, as well as examples that illustrate why real-time visibility and traceability are needed.
What is real-time visibility?
In the context of complex medical device software, real-time visibility means that when you view data in one system (e.g., a project management tool), you can see the corresponding data in other systems (e.g., ALM, PLM, QMS, etc.). The key is shortening the cycle time from weekly or daily consistency down to consistency within seconds so that the data you're viewing represents the true source of truth.
What happens when MedTech leaders lack software project visibility?
Imagine that a VP of Engineering at a medical device company asks a manager about the status of a software release. The release involves a software algorithm update critical for the product's upcoming regulatory submission. The VP asks, “Is the latest algorithm ready for testing, and has it been integrated with the new data pipeline?"
Due to a lack of real-time visibility, the manager must check with a team lead to gather accurate information. The team lead asks a developer, “Is the code ready?” to which they respond, "The code is finished, but we're waiting on additional testing." The team lead passes this information back up the chain without mentioning further details about the integration dependency.
The manager receives the answer that the code is "ready" but also hears about a delay in QA testing. They relay this partial information to the VP, "The code is complete, but there’s a slight delay in testing." The VP then assumes the code is almost ready for regulatory submission, leading to misplaced confidence in the release timeline. By the time additional details are communicated back up the chain, the VP has already informed executive leadership that the software release is on track. This misalignment between teams causes major delays in both testing and regulatory submission preparation. It can also cause understandable friction between teams.
Ultimately, the lack of real-time visibility leads to inefficiencies and a greater probability of errors and delays. Instead, what if the VP could easily view a dashboard of everything their teams are working on to determine how close each project is to release, what still needs to be tested, etc. at a glance?
Why is real-time visibility valuable?
Real-time visibility is valuable because stakeholders need transparency about what’s happening across the organization to inform time-sensitive decisions and deliver products to the market. Someone should be able to ask a product-related question and get an answer within a matter of seconds. This is not the case at most MedTech organizations — there is too much lag time between data production and data consumption due to the highly manual processes used to keep disparate tools “in sync.”
What is real-time traceability and how does it relate to visibility?
Real-time, end-to-end traceability means that traceability is automatically established across systems to instantly track changes and ensure no coverage gaps. Similar to real-time visibility, real-time traceability allows team members and stakeholders to access information across systems without going through multiple people or manual processes.
What happens when traceability is slow and manual?
Imagine that a medical device company is developing software for an implantable cardiac monitor. The software development team releases an update to improve arrhythmia detection, but they aren’t aware that the sensor integration team just changed the sensor's data format. Because the traceability matrix is updated manually, the developers are working with outdated assumptions about the data format.
The QA team then encounters multiple test failures because the software isn’t processing the sensor data correctly. Without real-time traceability, it takes several days for QA to trace the issue back to the data integration change, delaying resolution and retesting. While this is happening, the regulatory team prepares a design history file (DHF) for an upcoming FDA submission. Since they don’t have real-time traceability, the team unknowingly submits an outdated risk assessment that doesn’t reflect the latest software changes. This leads to documentation discrepancies, additional review cycles, and negative feedback from the FDA.
Why is real-time traceability valuable?
Real-time traceability is valuable because it helps organizations stay audit-ready without making employees spend a lot of time updating documents and meeting with colleagues. For example, a connected lifecycle management (CLM) platform like Ketryx automatically creates and maintains a real-time requirements traceability matrix that is always up-to-date with no manual work required. This enhances the organization’s compliance posture, reduces risk, and accelerates decision-making.
Top risks of manual data updates and disconnected systems
It’s risky for MedTech companies to continue relying on the status quo — manual updates and disconnected systems. Let’s take a look at some of the top risks, including:
- Data inaccuracy and integrity issues.
- Poor operational performance.
- Diminished collaboration and delayed decision-making.
Data inaccuracy and integrity issues
Manual data updates and synchronization between systems like Jira and Git can lead to inaccurate data and, ultimately, substandard product quality. Out-of-date, incomplete, or inconsistent data can also cause delayed issue identification and resolution, which results in prolonged development cycles and increased costs. According to the Systems Sciences Institute at IBM, the cost to fix a bug during the testing phase of the software development lifecycle is 15 times higher than the cost of fixing it during the design phase.
Additionally, inaccurate data leads to inadequate traceability, which makes it challenging to maintain consistent documentation and ensure regulatory compliance, potentially resulting in costly fines, product recalls, and/or legal issues. The ultimate risk of data inaccuracy and integrity issues is that an unsafe product reaches the market and ends up harming a patient.
Poor execution
Manual data synchronization between systems is labor-intensive and time-consuming, leading to higher operational costs and reduced productivity. It’s also slower, which means that you cannot count on data being up-to-date at all times as you would be able to with automated system connectedness. This can result in teams duplicating work and working on the wrong tasks, which leads to poor execution and lower quality.
Lower product quality and reliability due to inconsistent and delayed information flow can lead to customer dissatisfaction, reputational damage, and loss of business. This is especially true if inferior quality results in a product recall. A number of medical device software-related product recalls have already happened in 2024, each of which can cost a manufacturer hundreds of millions of dollars. Moreover, poor operational performance increases the risk of security vulnerabilities, breaches, and unauthorized access, which can lead to additional legal and financial consequences.
Diminished collaboration and delayed decision-making
Lack of real-time visibility and traceability hinders communication and collaboration, leading to misaligned goals and ineffective problem-solving. It also causes time lags between changes occurring and their communication to relevant teams, resulting in outdated or inaccurate information being used for decision-making. For example, a manager might report a project’s status to leadership using outdated data from manually updated systems, leading to decisions based on outdated information and further delays in execution.
Ultimately, manual processes and lack of system integration are not scalable, limiting the company's ability to handle larger projects or increased demand. This is because manually tracking changes across multiple teams — which can involve hundreds of people at large organizations — leads to increased bottlenecks that make it difficult for the company to grow.
Automated system connectedness: The key to real-time visibility and traceability
To overcome the risks of manual data updates and disconnected systems, companies need to close their existing visibility and traceability gaps. This will allow them to make high-quality decisions as quickly as possible and release products faster. The best way to do this is to leverage automation to connect the medical device software development systems (e.g., Jira, Git, eQMS, ALMs, etc.) that teams already use.
This type of automated system connectedness improves data accuracy and consistency by keeping it updated in near real time (i.e., a change in one system is immediately reflected in all other systems). It also provides connective tissue that creates relationships across systems and allows teams to trace updates from one piece of data to every other piece of related data to see the full impact of every change.
Obstacles to achieving optimal visibility and traceability without automated system connectedness
The uncomfortable truth is that it’s extremely difficult for medical device software companies to achieve real-time visibility and traceability with their current tools and processes. Top obstacles that stand in the way include:
- Manual data updates: Maintaining data consistency across disparate systems via manual updates (e.g., copying information from Jira and pasting it into a spreadsheet or requirements management software) is incredibly slow, inefficient, and error-prone. The cycle time between data changes and when the information is updated across all relevant systems is nowhere close to real time.
- Exponential complexity: As the number of systems and connections grows, the complexity increases exponentially. Coordinating everyone needed to monitor each system and keep things in sync quickly becomes unmanageable. This increases the risk of miscommunication, delays, and/or errors as teams struggle to maintain alignment across an increasingly fragmented environment.
- Lack of engineering bandwidth: Even if an organization wanted to build its own bespoke solution for system connectedness and automation, building and maintaining functional integrations for all the necessary systems requires specialized expertise. Most MedTechs don't want to dedicate crucial engineering bandwidth toward this type of work. In this situation, buying off the shelf is much more efficient and cost-effective than building your own solution.
Some companies may try to solve these obstacles by hiring more people to add data management bandwidth. But with more people comes the need for more meetings, emails, etc., further hindering productivity and scalability. Teams won’t be able to hit their goals, and dissatisfied employees may leave the organization altogether.
“Nobody wants to do things like traceability manually, but we still do.” - VP of Engineering, Fortune 500 medical device company
How to connect your systems for real-time visibility and traceability
Ketryx is an innovative CLM platform that allows companies to achieve the real-time visibility and end-to-end traceability required to ensure data accuracy and release products faster while staying audit-ready.
Ketryx easily integrates with existing development tools (e.g., Jira,) quality management tools (e.g., Polarion), and cybersecurity tools (e.g., Snyk) to automatically establish connections among requirements, risks, code, and tests across systems. This allows teams to see live updates and ensure compliance throughout the software development lifecycle without a lot of manual intervention.
“Ketryx has allowed us to channel our hardware and software engineers’ existing set of development, testing, and documentation practices directly into the generation of compliant documentation with minimal additional burden. This has allowed us to remain agile while delivering high-quality products.” – Alexander Chan, VP of Analytics and Machine Learning at Beacon Biosignals
See how Beacon Biosignals cut their release cycle time in half with Ketryx.
Using Ketryx yields benefits in several key areas:
- Speed: With the power of automated data updates, Ketryx unlocks visibility and traceability much faster than any group of humans assigned to the same tasks. This is important because data consistency within the organization is a key determining factor in how well your operations work, how quickly issues can be addressed, and how much collaboration is possible.
- Quality: By reducing complexity and providing guardrails that facilitate quality and compliance, Ketryx reduces the defect rate across the software development lifecycle. The platform natively ensures that developers follow QMS procedures — they’re prevented from breaking the rules set by the quality team.
- Expertise: Ketryx eliminates the need for internal teams to work on building and maintaining integrations for system connectivity. Because our team lives and breathes validated software development, you gain access to cutting-edge use cases and edge cases for CLM.
Gain real-time visibility and traceability across your SDLC
Real-time visibility and traceability aren’t just advantages — they’re necessities. Without them, organizations can face release delays, compliance issues, and even product recalls, all of which stifle growth and put patient lives at risk. A CLM platform like Ketryx is the best way to automatically connect systems to achieve the real-time visibility and traceability needed to accelerate product development, improve quality, and stay FDA-compliant.
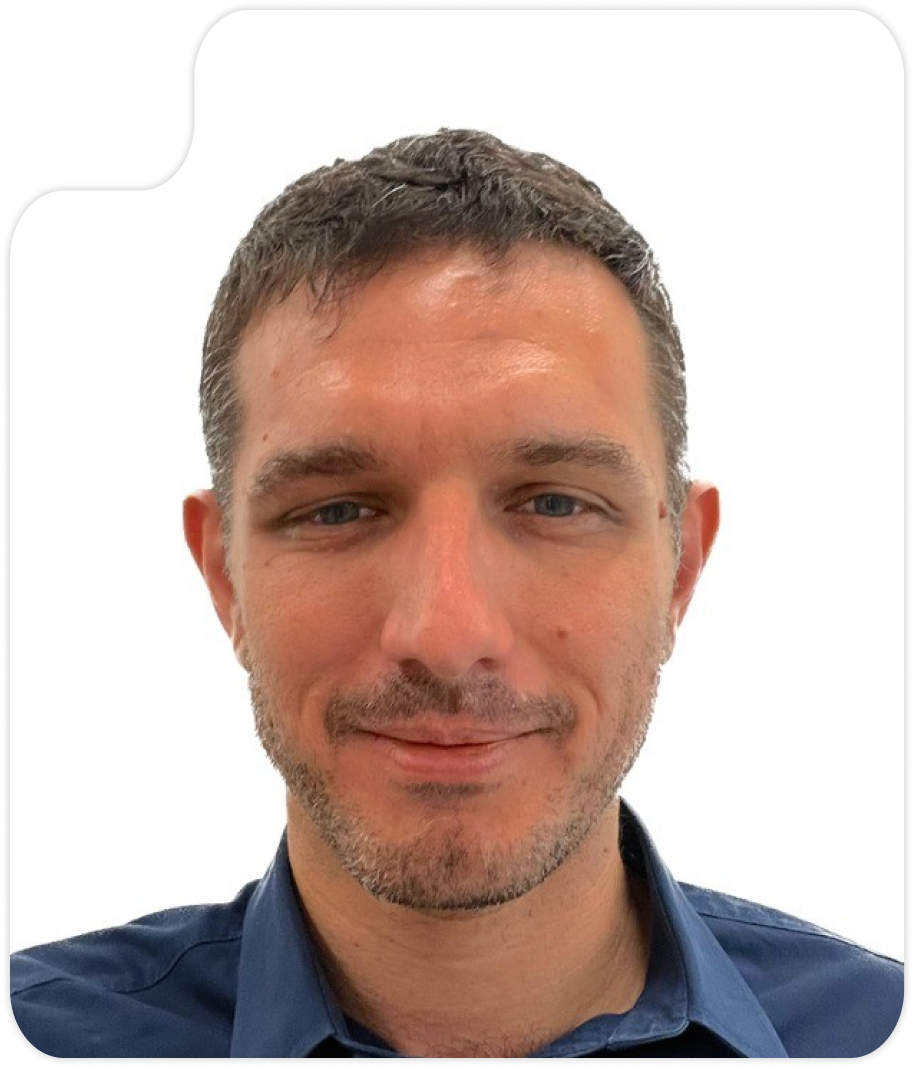
Jake brings experience that fuses technology and quality systems. His professional journey began in operations, fostering a deep understanding of complex, safety-critical systems; prior to Ketryx, he was a manager in a GMP pharmaceutical plant at Amgen. This foundation has profoundly shaped his approach to tech, where he currently serves as the Vice President of Client Operations at Ketryx. Jake holds an MBA in Operations and Logistics and a Master's degree in Systems Engineering from MIT, where he was a Leaders for Global Operations (LGO) Fellow.