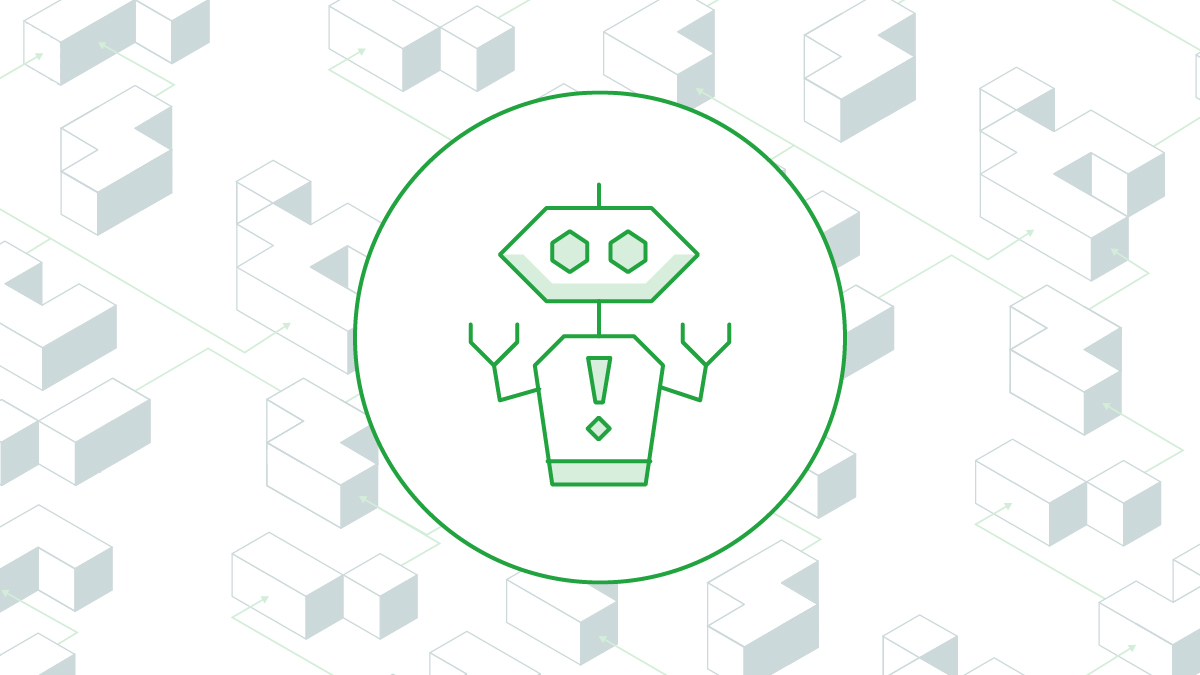
Why the FDA’s Most Common Warning Letter Might Surprise You
Table of Contents
The FDA (Food and Drug Administration) is responsible for ensuring the safety and effectiveness of food, drugs, and medical devices in the United States. The agency carries out this mission by inspecting facilities and reviewing products to ensure that they meet appropriate standards. Well known cases include tales of the FDA padlocking warehouses and shutting down manufacturing entirely and seizing products because of the perceived dangers. Other lesser known cases have included long-term health issues and even patient deaths.
So with all of these dramatic consequences, you might be surprised to hear that the most common reason for an FDA warning letter is the failure to follow standard operating procedures (SOPs). In the fiscal year of 2022, 42 warning letters were issued. 23 of these addressed documentation and SOPs. In the world of safety-critical industry with so much at risk, how do so many companies fail to follow their SOPs?
What are SOPs?
Standard operating procedures (SOPs) are detailed instructions that describe the steps necessary to complete a particular task or process. SOPs are a critical component of quality management systems (QMS), which are designed to ensure that products and services meet customer requirements and regulatory standards. SOPs help to standardize your processes, reduce variability, and ensure consistency in the quality of output.
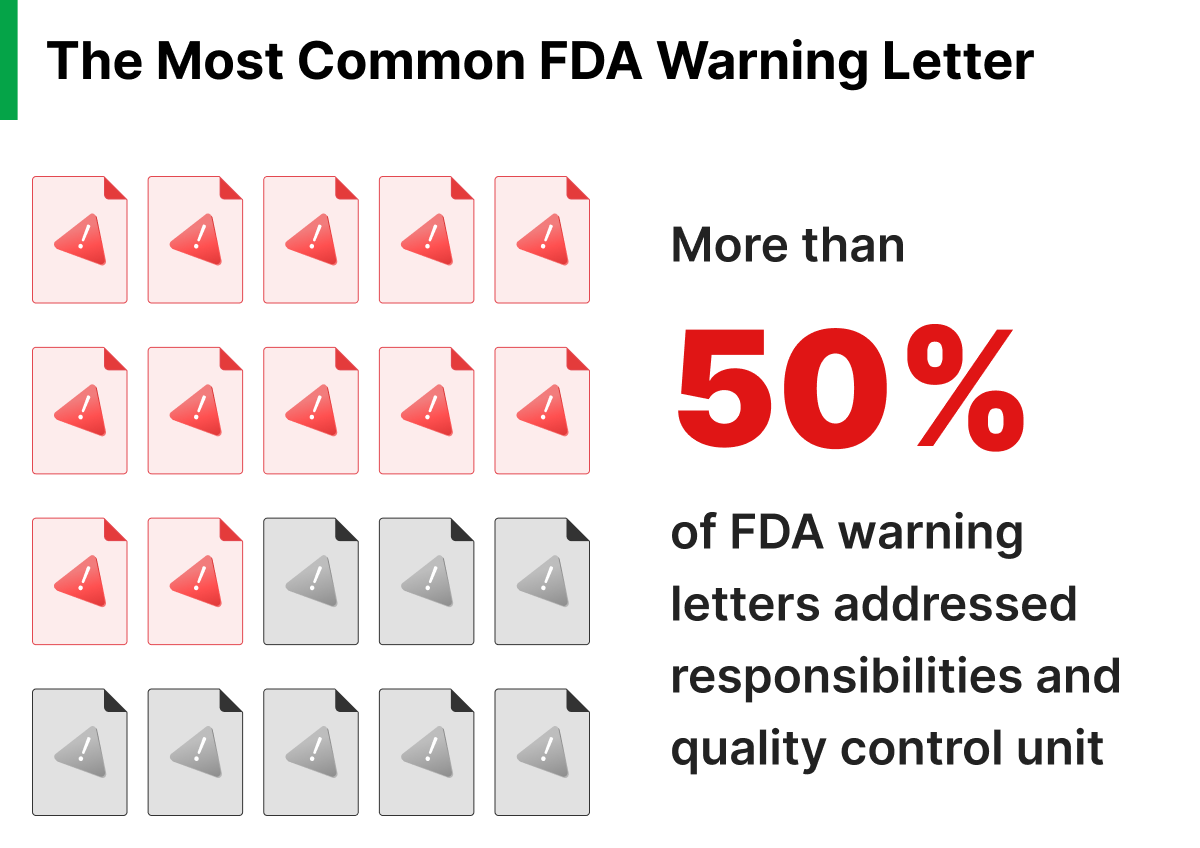
Why is it important to follow SOPs?
The FDA, like any organization, is limited in resources. The variety, complexity, and number of companies they must review for surveillance is huge. This burden results in most inspections lasting no more than a few days. Therefore, the agency takes a very efficient and risk-based approach to inspections.
The FDA’s thought process looks something like this:
- I have two days to inspect this big company that consists of hundreds or thousands of people, and I know nothing about how this company specifically operates or any of the people here.
- The quality system is meant to manage all other subsystems and keep them in compliance.
- Therefore, I will spend most of my time checking the quality system.
- The foundation of the quality system is a set of SOPs that are, presumably, meant to be followed by everyone in the organization to ensure compliance with regulations.
- Therefore I will rigorously check to see if SOPs are being followed.
The FDA knows if a company doesn’t take compliance seriously, they certainly don’t take patient safety seriously. The fastest and easiest way to know if a company takes compliance seriously is checking to see if they follow SOPs.
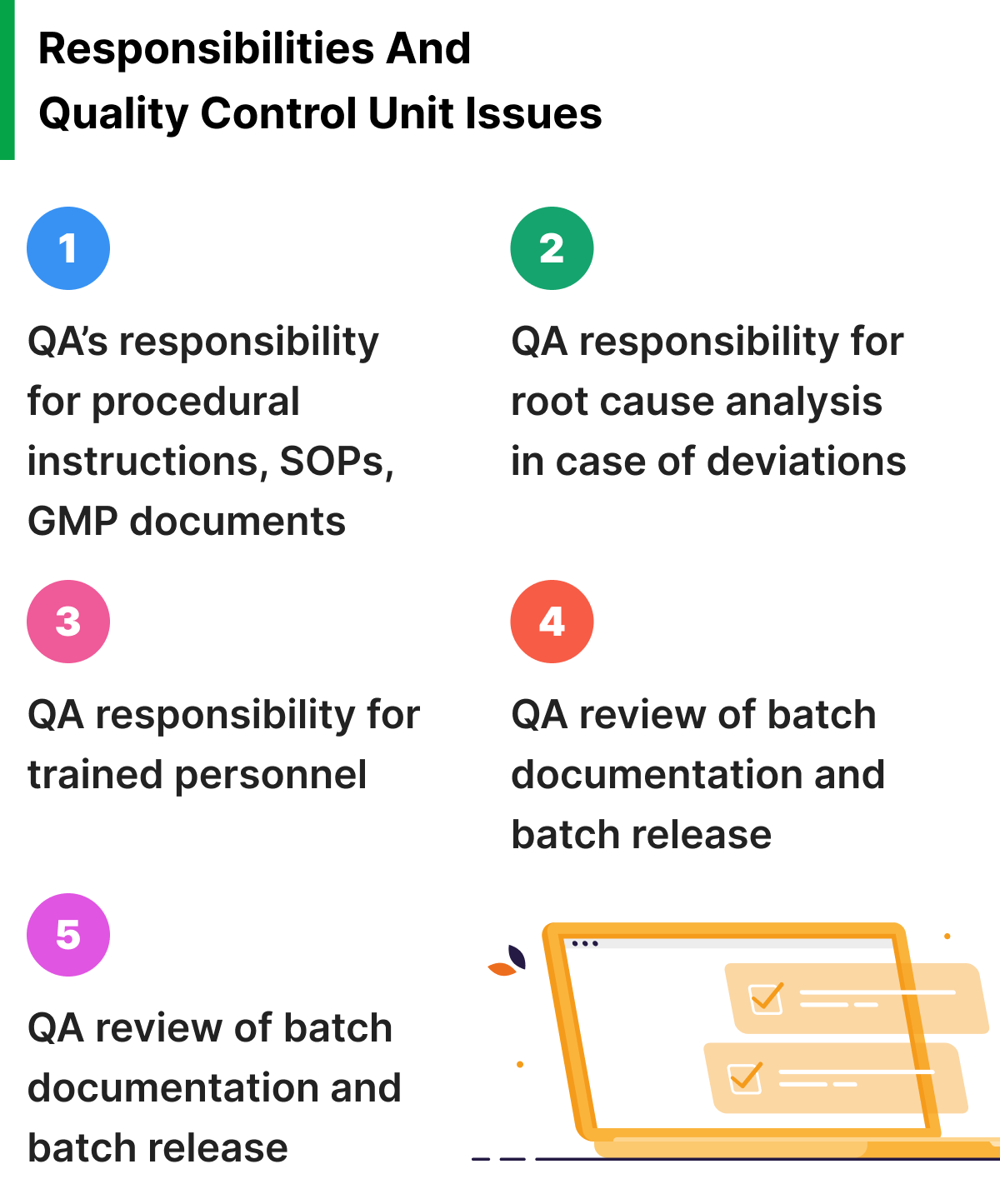
So, failure to follow SOPs can result in serious consequences for your company, including FDA warning letters, product recalls, and legal action. When your company fails to follow its own processes, it increases the risk of product defects, adverse events, and safety issues. On top of scrutiny from the FDA, failure to follow SOPs can lead to inconsistencies in the quality of output, damaging your company's reputation and eroding customer trust.
Why do companies fail to follow their SOPs?
- Lack of awareness: Your team members may not fully understand the importance of following SOPs, or they may not be aware of the specific procedures that they are required to follow. This oversight is not entirely the employees’ fault. Product and quality managers can address these mistakes through training and education programs that emphasize the importance of SOPs and provide clear instructions for following them.
- Inadequate documentation: Without clear and concise documentation, your team may not have the necessary guidance to follow SOPs effectively. You can address this issue by developing detailed SOPs that are easy to understand and follow, and ensuring that they are readily available to all team members.
- Failure to prioritize quality: Many companies fall victim to prioritizing speed or cost savings over quality. This shift leads to shortcuts being taken or processes being skipped, which can result in noncompliance with your SOPs. To address this, you must prioritize quality as a core value and ensure that all employees and management understand the importance of following SOPs.
Whether you follow standard operating procedures (SOPs) or not can have serious consequences for companies, and roughly 50% of warning letters the FDA hands out addresses this issue. To create safe software, it’s critical to follow procedure and, above all, do what you say you are going to do. Addressing the root causes of noncompliance with team training and management priorities can ensure that your products and services meet customer requirements and regulatory standards while building customer trust and ensuring the safety and effectiveness of products.
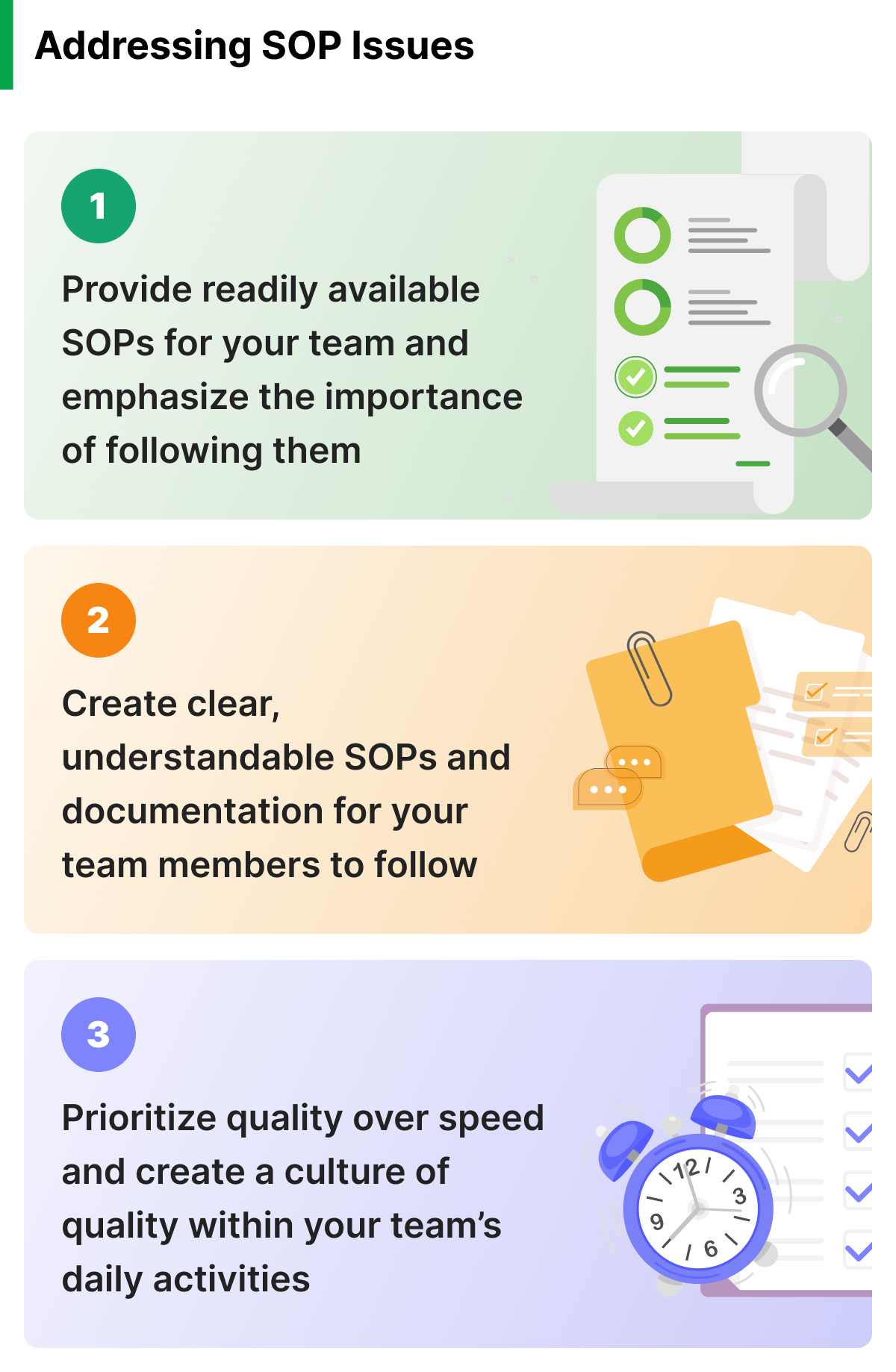
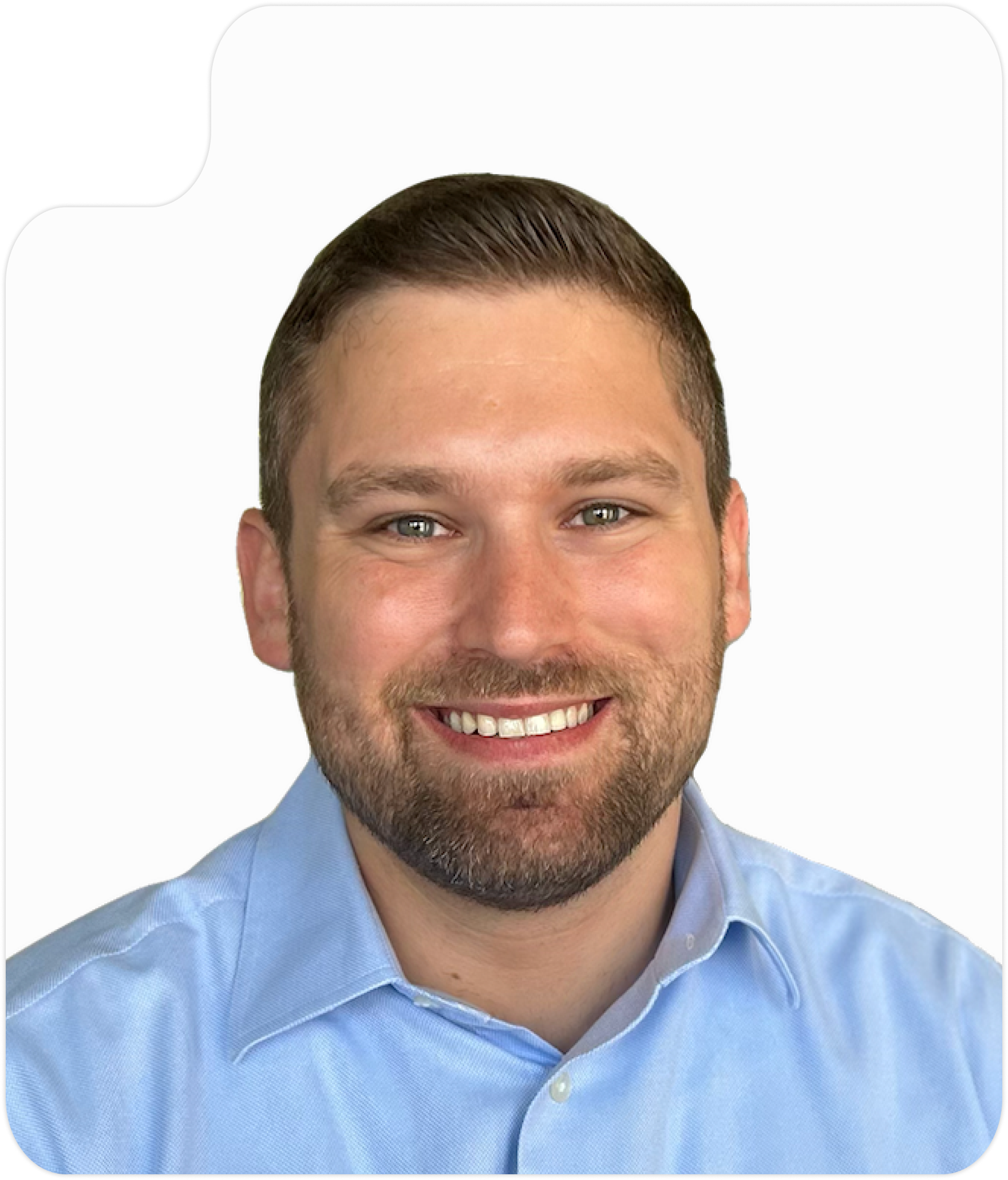
Erez is passionate about improving patient care and health outcomes with software solutions. Over the last decade, Erez worked in industries including computational mathematics, biotech, and energy, helping build monitoring systems for pharmaceutical equipment and AI for medication management. Before Ketryx, Erez worked with Amgen, the world’s largest biotechnology company, as the head of AI/ML for their medical device division and with Wolfram Research, the builders of Mathematica and Wolfram|Alpha. Erez holds a Master of Science in Electrical Engineering and Computer Science and a Master of Business Administration from the Massachusetts Institute of Technology.